“We now use a simple system to buy not only the piece of paper, but also the pens, the chair, and everything else the employee needs. Including the grinding wheel, the cutter knife or the gloves in the workshop,” says Al-Sahwi.
Schmidtsche Schack, a specialist in process gas cooling systems from Kassel, shows why e-procurement needs an ERP connection using the simple system e-procurement platform.
What do a welding robot and indirect purchasing have in common? They exemplify various digitization programs from Schmidtsche Schack, a Kassel based manufacturer of process heat transfer solutions and part of the Arvos Group. The head office employs around 280 people. Not only is the administration located there, but also the production hall. In both areas, there are numerous orders each year, whether for C-parts for manufacturing or for materials for indirect purchasing. In the past, this was time-consuming and costly due to paper-based orders, which involved a long administrative process involving checks and approvals. Rauad Al-Sahwi, Director Supply Chain Management at Schmidtsche Schack, set the ball rolling to finally optimize processes through a digital solution.
The right connection
The main aim was to connect simple system and the established ERP system SAP so that the entire ordering process could be carried out in the future via a user interface and without changing the systems. This is made possible with the simple system cockpit connection.
According to Al-Sahwi, we now not only buy the piece of paper, but also the pens, the chair and everything else the employee needs, including the grinding wheel, the cutter knife or the gloves in the workshop.
There, he can access the catalogues assigned to him and search for the right grinding wheels using a search term. The system then shows him one or more articles from which he can choose. With the required quantity, it goes to the shopping cart. Thanks to predefined rules, the customer can now only select a delivery address defined for him. As soon as the shopping cart is sent, the manager receives information that the shopping cart is ready for approval and can grant or reject it with a mouse click. When approved, an overview of the order with all necessary information is then transferred to the SAP system. The next step is delivery. Here, too, information such as the invoice is transmitted directly digitally and automatically compared and assigned with the order number. In total, Al-Sahwi expects a time saving of 30 minutes per order.
If an employee needs new grinding wheels, they simply log in via the user interface of the e-procurement solution, explains Andre Vieth, Strategic Buyer at Schmidtsche Schack.
If you want
Independent purchasing instead of Maverick buying
A major advantage for the company is also the definition of different user groups, for which tailored shopping cart limits and authorizations can be specified. This prevents individual paper orders for a few euros, for example. This creates trust in processes and employees. In this way, departments other than purchasing are also empowered to execute orders directly within their defined framework, if necessary. Schmidtsche Schack is constantly optimizing these authorizations so that processes can be further automated. This not only reduces process costs, but also creates transparency.
If you want
Impress users with intuitive interfaces
But employee involvement and feedback was also decisive at the beginning. For this reason, the system was initially rolled out directly in the purchasing department on a smaller scale and later extended to the specialist areas. They appreciated the fact that a solution was now offered with which ordering processes could be carried out leanly and quickly — a real added value in everyday working life and not senseless digitization.
The next step was much more exciting, to connect the sector that dominates in terms of costs and volume: manufacturing. The initial scepticism whether the system would be just as well received by so-called “BlueCollar” workers proved to be unfounded. This is because the user-friendly interface of the e-procurement solution, which is familiar in everyday life from the online shopping sector, benefited plant workers, who were otherwise less involved in digital processes.
The way to add something to the shopping cart is not revolutionary, but a well-known, proven solution. In this sense, acceptance also increased, according to Vieth.
Since the process was not rocket science, the workforce could be quickly converted to the new system. She was also trained with documentation on how to use the system. As a next step, the Düsseldorf location is to be connected to the e-procurement platform.
If you want
Of welding robots and digital natives
But digitizing purchasing is not the only digitization project at Schmidtsche Schack. In this way, the company wants to become paperless in the future. The people of Kassel have already taken a first step towards this by converting the formerly partly paper-based order requirements (BANF) to a completely electronic process. Another concern is to digitize tenders, i.e. to enter the area of e-auctions. In order to actively drive these projects forward, the company has created the position of digital officer within IT.
With regard to the future and young talent, companies also benefit from positioning themselves digitally and in a modern way. This is because the following generations, often referred to as “digital natives” because they are already growing up with digital tools, are attracted by modern equipment and digital solutions.
This also includes the latest technology in the factory halls. This is because, like many skilled trades, manufacturing is suffering from a shortage of skilled workers and a few up-and-coming talents who are interested in a training position. With five training places filled in the industrial sector per year, Schmidtsche Schack is looking forward to the challenges of the shortage of skilled workers somewhat more calmly. How is that possible?
One reason could be digitization efforts, which have an impact on the company's attractiveness vis-à-vis young talent. Although there is still a need for people who enjoy traditional crafts, with electrodes in their hands and a welding career ahead of them, Al-Sahwi sees an interesting development towards digitization. For example, a welding robot has already been introduced which can take over work but must be programmed by employees. This requires appropriate additional training for welders.
For employees, it is a positive argument that traditional crafts are combined with digital tools. We are also driven by the “digital footprint”. We have huge potential there and we are far from where we want to go, according to Al-Sahwi.
Trainees also benefit for their future career if they are introduced to digital tools as early as possible.
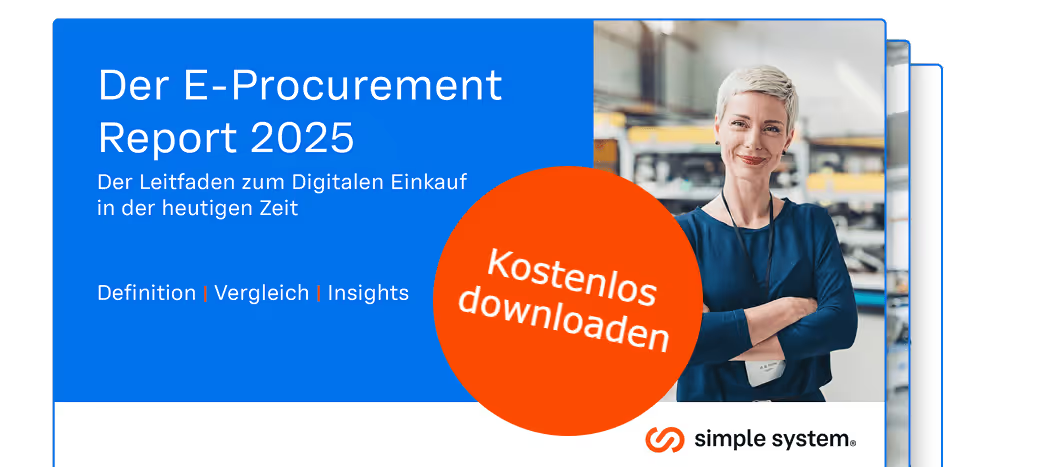
Einkaufen & sparen
Erfahren Sie, wie es geht, in unserem kostenlosen E-Procurement-Report. Jetzt kostenlos und unverbindlich herunterladen.
Jetzt lesen