Process costs are not really perceived by many companies. In doing so, they can achieve disproportionate dimensions, especially when procuring C-parts. These mostly hidden costs can be avoided thanks to automated processes.
A comparison between traditional and modern processes shows how high the advantage can be for companies. All costs associated with operational processes and which can be attributed to them can be recorded as process costs. That's the theory of business administration. In practice, process costs in companies often go unnoticed. However, an analysis of process costs is particularly worthwhile when procuring C-parts, as these can significantly exceed the value of the items and goods required for the day. Using a specific example, we would like to illustrate how great the contrast between process costs is in the classic procurement process compared to a procurement platform.
Cost trap of classic procurement processes
C-parts usually have only a low value in goods, but are essential for operational processes. Their procurement typically results in extremely high process costs. This is because in many companies, the procurement process is still carried out in traditional ways and with numerous manual processes. Let's have a look at this — and calculate what this means in terms of costs.
- Requester Mr. Dreher urgently needs square screws. He quickly searches in the catalogue (print or online). Before ordering, he must create a requirement request (BANF) in SAP. All this costs him15 minutes working time.
- The square screws are — due to current delivery problems — more expensive than usual. Therefore, Dreher's boss must review and approve the purchase. Fall for this 5 minutes working time on.
- Controlling now checks whether all data (such as account allocation) is correct before it triggers the requirement in SAP. Working time: 5 minutes.
- The BANF is now converted into an order and checked by the purchasing department for price and delivery date. In addition, purchasing inquires with the vendor regarding availability and delivery date. Create an order: 5 to 10 minutes, request: 20 to 30 minutes.
- The vendor should now send an order confirmation. If he does not do this, the shopping department will remind him of them. Working time:5 to 10 minutes.
- The goods arrive a few days later. The incoming goods check whether the correct screws have been delivered in the ordered quantity. The receipt of the goods is recorded in SAP and Mr. Dreher is notified that his screws have arrived. Working time:15 minutes.
- Finally, financial accounting checks the invoice and records it. Approval may require clarification of discrepancies regarding the price and other factors. Effort: 10 to 15 minutes.
- Conclusion:In the worst case, the processing time for all process steps amounts to a total105 minutes— a full 1 hour 45 minutes per order. Assuming an internal hourly rate of 70 euros, the process costs here are 122.50 euros/hour. Depending on the exact processes of the company, the costs are open at the top.
Optimized processes thanks to procurement platform
And now the procurement platform in direct comparison:
- Requester Dreher quickly finds the right square screws using a search term in the online catalogue of the procurement platform. He adds them to the shopping cart. This, together with the account assignment data, is transferred directly to the ERP. A BANF is automatically generated there. Working time: 5 minutes.
- The square screws are — due to current delivery problems — more expensive than usual. Therefore, Dreher's boss must review and approve the purchase. Working time: 5 minutes.
- Since the account assignment data was automatically transferred to the system, Controlling no longer needs to check them.
- The BANF is automatically converted into an order by the system — all important data for this has already been transferred from the online catalogue.
- Purchasing only checks the delivery date of the order confirmation. Working time: around 5 minutes.
- The goods arrive a few days later. The incoming goods inspection is carried out in SAP. Mr. Dreher is notified that his screw has arrived. working time:15 minutes.
- The invoice is automatically checked in ERP. This is possible because prices and conditions are transferred directly from the online catalogue to the system. This reliefs financial accounting of the audit.
- Conclusion:Thanks to the automated process, the processing time for all process steps is approx.30 minutes. Assuming an internal hourly rate of 70 euros, the process costs for an order are35 euros/hour. This gives the company around 70 percent saved time and process costs!
Our example makes it clear that it is worthwhile to have a closer look at internal procurement processes and evaluate them. It can be worthwhile to use a procurement platform, not only in terms of lower costs. In times of a shortage of skilled workers, it helps to simplify processes and reduce processing times. In this way, employees in the individual departments can be deployed more precisely for other tasks or redundant processes can be eliminated. As a result, companies not only benefit from lower costs, but also from improved efficiency.
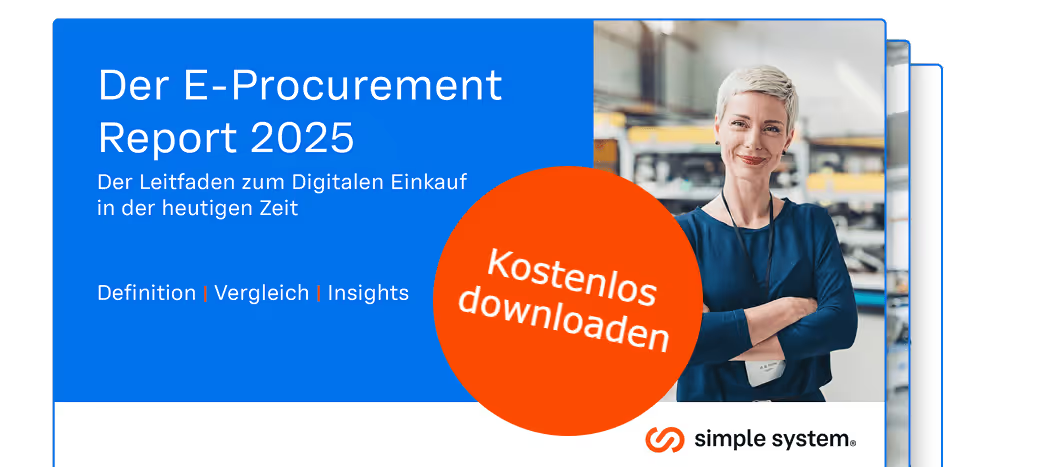
Einkaufen & sparen
Erfahren Sie, wie es geht, in unserem kostenlosen E-Procurement-Report. Jetzt kostenlos und unverbindlich herunterladen.
Jetzt lesen